In the coatings and ink industry, bubble problems are generally considered unfavorable and need to be eliminated.
It is important to identify the source of the bubbles in order to choose the appropriate defoaming agent or adjust the application process to minimize bubble formation.
2. Mechanism of bubble generation
In a system composed of pure liquid, foam cannot exist stably for a long time, and will soon spontaneously break under the action of gravity even if it is generated. However, once the system contains some surface-active agents, bubbles may be stabilized at the surface under the help of surfactants, resulting in various foam problems. To solve the bubble problems caused by the above reasons, in addition to choosing suitable raw materials and appropriate operating conditions and processes to minimize the generation of bubbles, adding various types of defoamers is the main method in the coatings and ink industry to solve foam problems.
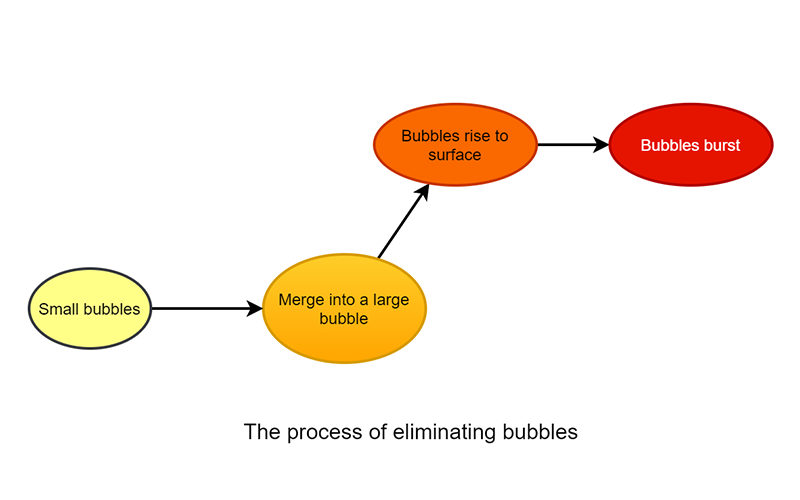

If a compound can be used as a defoamer in a particular system, it needs to meet two conditions:
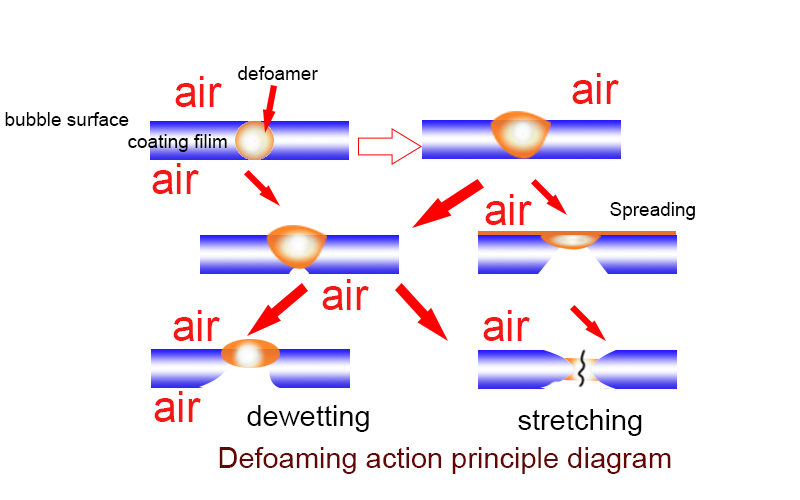
The defoamer that meets the above conditions, when added to the system, penetrates and wets the foam film by dispersing into it, ultimately destroying the foam film and achieving the defoaming effect. The specific principle is shown in the figure left.
Defoaming Ability and Compatability
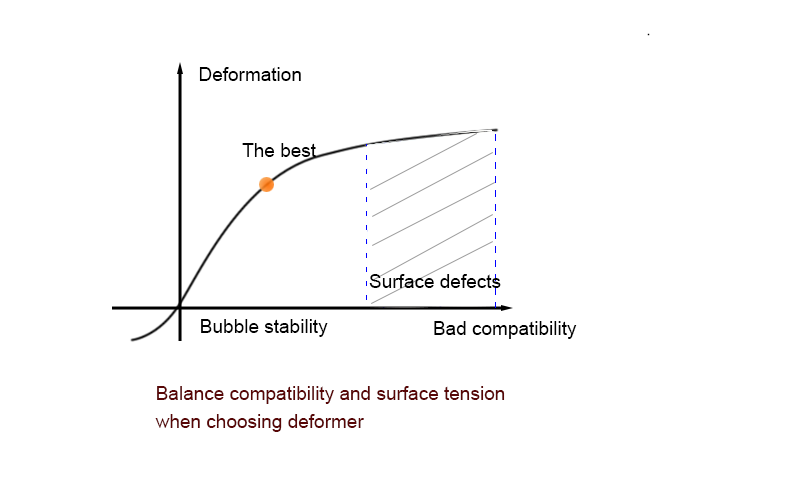
The defoaming ability of a defoamer depends on two factors: the incompatibility between the defoamer and the system, and the surface tension of the defoamer itself, which can be adjusted through molecular design.
For a particular system, the selection of defoamers is usually not the stronger the better. According to defoaming theory, excessive defoaming ability is usually accompanied by excessively low surface tension and poor compatibility, which are often the sources of many coating defects.
Therefore, for a particular system, the most suitable defoamer should have its incompatibility with the system controlled to a level that does not cause coating defects. The optimal point for defoamer selection is often in this area. At this point, the defoamer has the strongest defoaming effect and comes with safe and reliable usage performance.
3. Types of defoamers
Due to the significant differences in the chemical composition and physical properties of coatings between solvent systems and water-based systems, there are also significant differences in the defoamers suitable for solvent systems and water-based systems
3.1 Solvent based defoamer
Due to the low surface tension of silicone compounds and their incompatibility with most resin systems used in coatings, silicone defoaming agents are extensively used in the paint industry. The silicone defoaming agents typically used in paint formulations are modified silicon compounds.
Because of the low surface tension and incompatibility of the silicone segments, silicone defoaming agents are often more efficient than non-silicone defoamers. They can function at lower addition levels, and the amount needed to achieve sufficient defoaming effect is often not enough to cause a change in the system’s transparency. Therefore, silicone defoaming agents are widely used in high transparency topcoat systems while maintaining good defoaming performance.
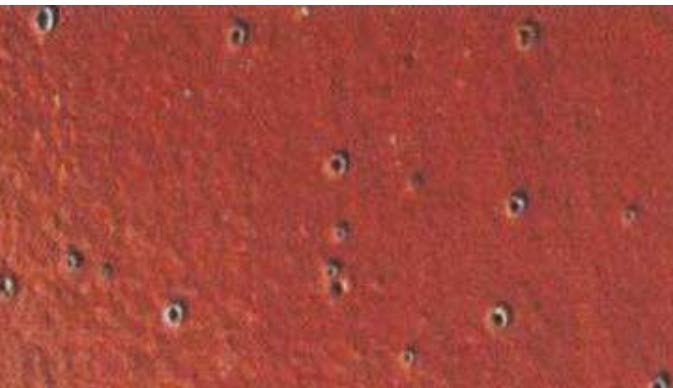
NOTED: due to the low surface tension of silicone defoaming agents, substances in the paint system that are incompatible and have low surface tension are often the main causes of film defects. Therefore, the use of silicone defoamers often requires special attention to their safety of use (such as tendencies to cause shrinkage holes, effects on re-coating, etc.)
With varying concentrations, silicone defoaming agents are generally classified into two major categories: solution-type and concentrate-type. Solution-type defoaming agents are convenient to handle and easy to add, while concentrate-type defoaming agents have strong defoaming power. The table right summarizes the use of DCA’s silicone defoaming agent products in solvent-based systems
3.2 Water based defoamer
As environmental protection requirements continue to rise, the development of water-based coatings is increasingly emphasized. Due to the high content of surfactants in water-based coating formulations, the issue of foam stability is more severe compared to solvent-based coating systems, which in turn leads to higher demands for defoaming agents. Like solvent-based coatings, defoamers for water-based coating systems are chemically divided into two main categories: silicone-based and silicone-free.
From the perspective of physical form, they are divided into three main types: emulsion, solution, and concentrated.
- Emulsion Defoamers:
- Advantages: Pre-dispersed in small droplets; no need for grinding; quick action; convenient and can be added at any stage.
- Disadvantages: Not suitable for high shear environments; can cause demulsification.
- Concentrated Defoamers:
- High active substance content; requires smaller dosages.
- Adjustable defoaming strength by altering the hydrophilic parts of the silicone oil structure.
- More effective than emulsion defoamers in eliminating microfoam; ideal for high viscosity water-based systems.
- Solution Defoamers:
- Require good dispersion for optimal performance.
- Need to be grinded under high shear force during use.